真空浸炭炉メーカー ×
金属熱処理会社 対談
真空浸炭炉の未来について語る
株式会社不二越 サーモテック事業部
シニアエンジニア 町 哲司
株式会社不二越 西日本支社
工作機営業部 桔梗 秀紀
株式会社松徳
代表取締役 横尾 臣則
- TOPページ 〉
- 真空浸炭炉の未来について語る
誕生のきっかけは、ヘリボーン作戦!?
松徳:はじめに、真空浸炭炉の誕生した背景っていうところからお聞かせください。どのようなニーズがまずあって、どのような技術革新があった後に、現在のような真空浸炭炉が誕生したのか、その辺から・・・
町:私も先輩からの又聞きで、確認はとっていないので恐縮ですが、もっともらしい真空浸炭技術開発の逸話がありまして。何かというとベトナム戦争なんです。ベトナム戦争の時に、ヘリコプターの部隊いわゆるヘリボーンをアメリカ軍が大規模に展開したんですね。
松徳:ヘリコプターの部隊ですか。
町:ヘリコプターに兵隊を乗せてジャングルへ行き、そこで兵隊を降ろす。そういう作戦をベトナムで大規模にやったんです。その時に地上から攻撃されるでしょう?その機銃弾がヘリコプターのギヤボックスに命中し、オイルが漏れる。オイルが漏れて潤滑が出来なくなった状態でもローターを回さないといけない。不時着までの数分間だけ飛べるようなギヤボックスを作らないかんと。
松徳:まさに命がけ、着陸できるかどうかのレベルですよね。
町:オイルが漏れてもなんとか避難して安全なとこに引き返す、というニーズが生まれた。そしてその時のギアですが、当然その時から『浸炭』という技術はあったんですが、無潤滑で歯面が高温になっても強度が落ちにくく、焼き付きしにくい表面処理ということで高濃度浸炭が適していると考えたと聞いています。高濃度浸炭するためには、ガス浸炭では、なかなかその表面に多くの炭化物を形成するのが難しい。真空浸炭だと生ガスを直接導入するので、表面に炭化物が形成しやすいと。それが真空浸炭炉を開発するきっかけになったというふうに聞いてます。
松徳:真空炉自体は前からあったんですね?
町:日本で真空炉が普及し始めるのは1970年代ぐらいですかね。それ以前は、真空炉はあったけれども、浸炭には利用されていなかったんです。その当時浸炭は、固形浸炭、液体浸炭、ガス浸炭が主流でした。いわゆる高濃度浸炭させる面倒くささ、難しさがあったんです。そこで真空炉で浸炭しようということになったんですが、当初の原料は、米国で豊富な天然ガスだった。天然ガスはメタンの含有量が80%以上です。メタンは安定したガスなんで、結構大量のガスを入れないと浸炭しない。いいものができるんですけども、同時に大量のスス(煤)が出て、真空炉の加熱室がコークスまみれになる状態で運用していて、このススの克服が課題だった。たまたま軍需があって「そりゃ、もう早いことなんとかしないとあかんぞ」っていう状況に追い込まれて、真空浸炭で高濃度に浸炭しなければいけないような状況が生まれた……。まぁ、きっかけは多分他にもあったと思いますが。
ガスを制するものが、浸炭を制する!
松徳:ヘリボーン作戦が起点とは、なかなか興味深いお話ですね。真空浸炭炉を現在のように運用する上で、核になる技術っていうのはどういうところだったんですか?その技術があったから実現できた、みたいな……。
町:結局、今お話ししたように、ススが出るか、出ないかというところがポイントになるんです。例えば、製品処理する時に10の炭素が欲しいと思って10のガスしか入れないと、絶対10は入らないんですね。原料ガスが100%の効率で処理品表面にまんべんなく命中しませんから。必ず外れが出ますから。だから、10の炭素が欲しい時は30とか40ぐらいの原料ガスを入れないといけない。10入ったとすると残りの20とか30のガスが必ず余りになる。その余ったのが、ガスの状態で真空ポンプによって外に全部抜ければいいんですけれど、実際は一部分の量が抜けずに分解・重合などでススになってしまう。
松徳:そこで原料であるガスに目をつけたと?
町:真空浸炭の大きなネックがススへの対処です。細かいところはちょっとさておき、ガスの使い分けによってススが出ないというか、抑制が可能になった。それによってメンテナンス性が大幅に向上したんです。現在は真空浸炭のプロセスで、世界的に見ると一番多いのはアセチレン。それと、フランスなどヨーロッパのメーカーは以前からプロパンガスです。
松徳:ガスによって、ススへの対処が変わり、メンテナンス性も変わったと?
町:そう、それまでは先ほどお話ししたように、本当に開発初期の頃の真空浸炭炉だと、断熱材とか炉の中に、本当にびっしり岩のようにスス、カーボンがこびり付いていた。私なんか本当に手でやっても全く取れなかった。タガネで、ハンマーで叩き落とすようなことを、もう毎週もやってました(笑)。それが、そこまでしなくていいようになったことが大きいですよね。
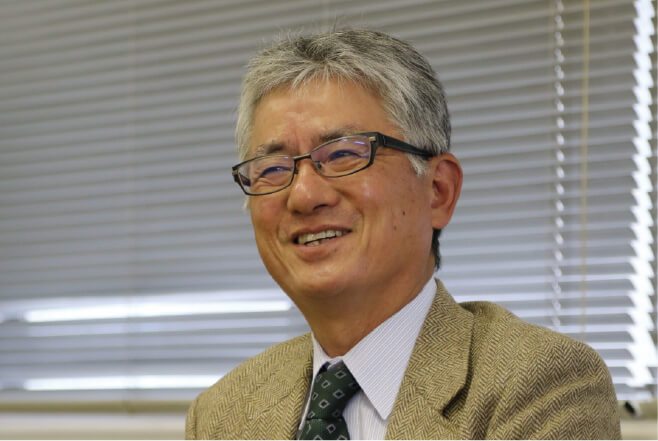
株式会社不二越 サーモテック事業部
シニアエンジニア 町 哲司
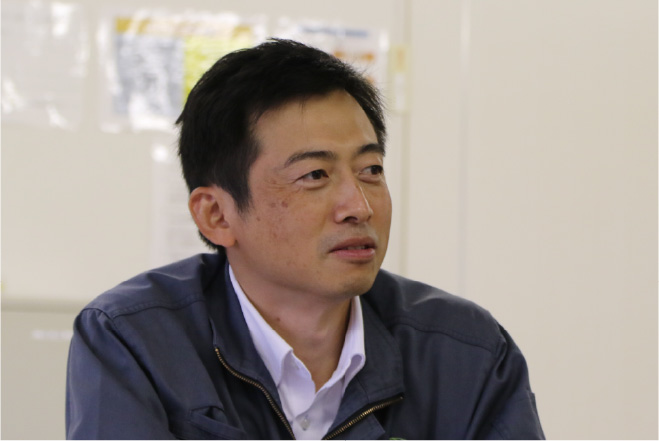
株式会社松徳
代表取締役 横尾 臣則
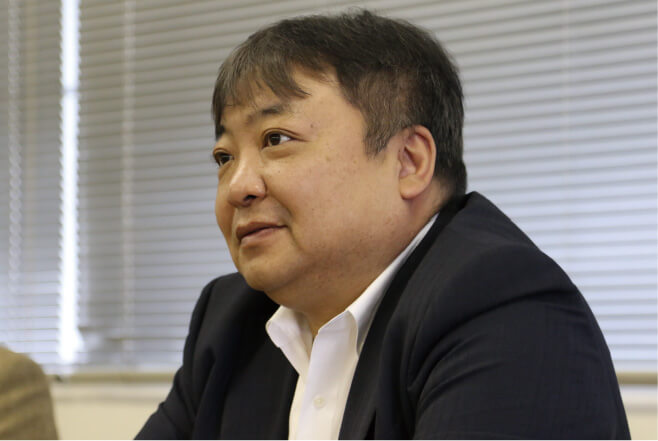
株式会社不二越 西日本支社
工作機営業部 桔梗 秀紀
ススからヒーターを守れ!
松徳:御社(不二越)は真空浸炭炉の開発において、どのような課題、テーマを設けられて、また、どのようにそこを克服されたのか聞かせてください。
町:スス(煤)については、アセチレンを用いることで随分改善されたけど、ゼロにはならない。必ず、わずかなススが出るんです。エチレンだとちょっと条件が変わりますが、やっぱり炉のヒーターとか、端子にススが影響を与えるんです。真空容器の中でヒータートラブルが起きると、中が冷えるまで待ってから修理に入らなければいけなかった。特に高濃度浸炭処理の時は、普通の浸炭よりガスを多く使うので、やはりススが出やすい。それがデータでもはっきりしてきた時に、従来の構造のままではとてもお客さんに勧められないというふうに判断しまして、ヒーターの構造そのものを変えたんです。弊社の真空浸炭炉は後発なんですけど、割と早い時期にヒーターの構造には着目していました。さらにヒーター自身を浸炭のガスが全く触れないように早い時期に設計変更しました。
松徳:なるほど。
町:松徳様に納入しているNVC-10ST型で言うと、加熱室の天井部分から内部に向かって、左右6本、合計12本のセラミックラジアントチューブを差し込み、その中にカセットヒーターを各々落とし込んで、チャンバー内の製品を加熱しています。
松徳:1000℃を超える熱をラジアントチューブで伝えるということなんですけど、ヒーターやチューブは普通のガス浸炭の常識だと交換のタイミングが来るわけですよね?
町:それはよく聞かれる質問ですが、弊社製の同じ構造の真空浸炭炉で一番長生きしてるのは18年です。
松徳:18年間もヒーターやチューブの交換なしですか?
町:はい。これがいいのは、直接的な消耗部品費用が削減できるだけでなく、交換の費用や、突然ヒーターが悪くなって、せっかく生産している途中にそういうことになると、部品を交換するのに一度止めなきゃいけない。その停止期間が2日以上も。それを避けられるところが大きいでしょう。幸い、改良後ヒータートラブルは皆無といってよいです。
松徳:全くそう思います。御社の真空浸炭炉の特徴、大きなところを聞かせていただいたのですが、当社については3室型の真空浸炭炉は非常に珍しいもので、その特徴についてちょっと聞かせていただけますか?
1トンの壁に挑戦!
桔梗:3室型の真空炉というのは、3室だけで見ると珍しくはない。ただ、1トンの焼入れができる3室いうのはそんなにない。横尾社長からも炉の設計に着手する前に、まず、1トンという処理量の真空横型バッチ炉としては、非常に大きい、なおかついろんな処理が別々にできる炉が欲しいと。それは、ステンレス部品の高温浸窒硬化処理とか、ダイス鋼金型の加圧ガス冷却とか、大型部品の浸炭焼入れとか、更には、焼ならし、焼きなまし等その辺を考えてのご要望でした。
松徳:うちは熱処理屋なんで、やっぱりいろんなお客さんの要求があっていろんな商品を扱っている、扱わざるを得ないというところが、メーカーさん社内の熱処理の部門と違うところです。逆に言うといろんなものに対応できるような炉にしたい、まずはそこですね。炉を作られるメーカーさんからしたら、多分それは一番嫌だと思うんです。ある程度熱処理をする製品を限定してやるほうが作りやすいと思う。しかし不二越さんは、それに応えてくれた。
町:もう無理やりみたいな感じです(笑)。3室は珍しくないけれどやっぱり真空浸炭で1トンというところは……。小さな400キロぐらいのものはある。でも本当に真空浸炭がこれから喜ばれるであろう部品を処理することを想定すると小さすぎる。だから、やっぱり1トンで3室が欲しいと言われたら、実際、私どもも開発には慎重にならざるを得ないですが、やってみる価値があった。3室にすることで、真空浸炭以外のものもできるだけ取り込めるように設計しています。今回のNVC-10ST型は、多目的に重点を置いて設計していますが、その要点は以下になります。
1:エチレンガス・アセチレンガスの兼用が可能で、部材や処理に合わせて、ガスの特徴を活かして、切り替えが可能です。
2:浸炭シミュレーションで類似形状-複数種類の部品を事前選別し、混載の幅を広げられます。
3:加熱温度についていえば、最高使用温度は1100℃で、ほとんどの合金鋼、特殊鋼の加熱処理ができます。又、窒素ガス雰囲気加熱(雰囲気攪拌)ができるので、マルテンサイト系ステンレス鋼の窒化焼入れ処理など1000℃以上の高温で均一な浸窒処理が可能です。
4:浸炭1次冷却速度の多様化
油焼入れ(揺動)、2.9bar窒素ガス加圧ガス冷却、減圧ガス冷却は勿論、複雑形状、薄肉部品の1次冷却変寸抑制のための真空徐冷も可能です。
5:真空排気能力の強化
大型メカニカルブースター真空ポンプを搭載し、高真空側でのアセチレンガスによるマイクロパルス(短時間で浸炭―拡散を繰り返す)に対応できます。
松徳:ありがとうございます。それは御社としても、今後真空浸炭炉のニーズが高まってくるというお考えがあったからだと思います。御社として今後真空浸炭炉の将来性とか、可能性。その辺りは、どのようにお考えになられてますか。
時代が求めている真空浸炭!
町:まず、真空浸炭は、廃棄物、エネルギー損失がガス浸炭と比較して大幅に削減でき、省エネ、環境対策として金属製品製造業にとっては、非常に有用なプロセスです。
次に、高濃度浸炭・炭化物分散処理のニーズは、自動車部品、産業機械、建設機械を中心に伸びる余地が大きい。今後は小ロットの加工依頼なども増えると予想しています。
LCC(ライフサイクルコスト)面でも、休日さらには生産変動による急停止、立ち上げが容易で、停止期間中の設備の維持管理負担を極めて小さくできます。更にヒーターやラジアントチューブといった主要な消耗品も、寿命を大幅に延長できています。電力の消費割合は大きいですが、短期停止時の温度・雰囲気の維持が不要になります(休止温度・雰囲気維持エネルギー最小化)。少量多種類生産の対応では、特に省エネ、生産性改善効果が大きくなります。
大きな枠で考えれば、2015年国連サミットで採択された、2030年を年限とする17の国際目標「SDGs」に準じて、日本SDGs推進本部が取りまとめた優先課題で省・再エネルギーにおける「産業界が業界ごとに自主的に温室効果ガス排出削減目標を設定し、省エネルギーをはじめとした国内事業活動における排出削減に取組む」方針にも合致しているプロセス、設備と言えます。
松徳:まだまだ真空浸炭のニーズや可能性は広がりそうですね。ありがとうございました。
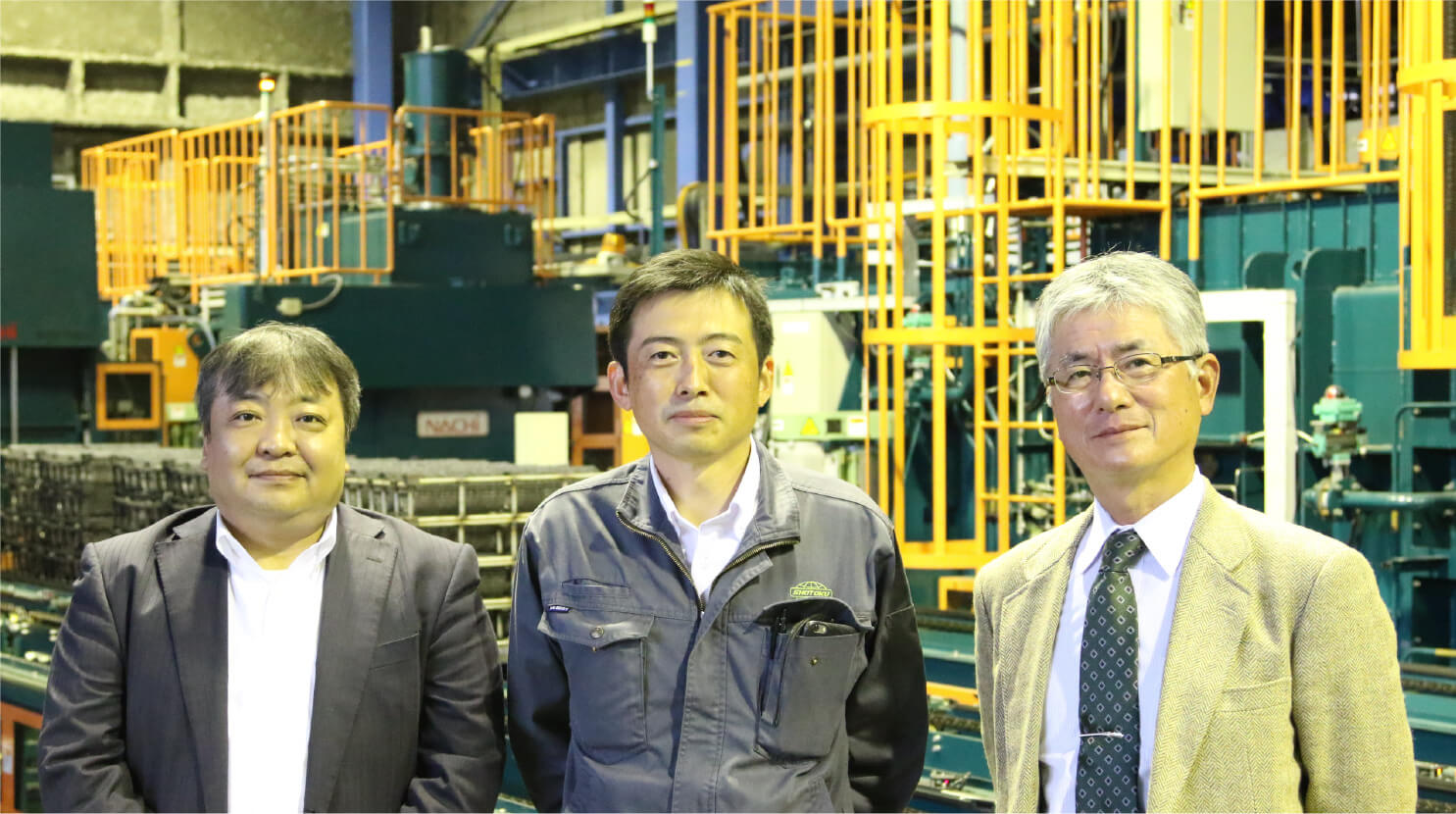
(左)桔梗 秀紀 (中央)横尾 臣則 (右)町 哲司